FREQUENTLY ASKED QUESTIONS
How will I receive my Order?
Most orders are shipped common carrier to business addresses as the cheapest option. We can also ship to the nearest freight terminal to your address if you do not have a business address that can be used. Residential deliveries cost an additional $ 35, so we do encourage using a business or freight terminal address in order to avoid the additional cost. Each order is well protected with plywood and/or cardboard, shrink-wrap, steel banding, on a pallet or in a veneer box if shipped via courier.
Do you Export?
We are able to deliver export packed orders to a freight forwarder anywhere in the USA or obtain ocean or air freight rates. We can also handle all necessary steps to ship our products to your door or desired port in your country.
What is Marine-Grade Plywood?
Marine-grade plywood is available in a domestic PS 1-95 (American Plywood Association) or BS1088 (British Standard Institution) standards. Marine-grade plywood made to the PS 1-95 is generally available in Douglas-fir. The grade of all plies of veneer is B or better, which means it may have knots, but no knotholes. Repairs are allowed and it is typical to see football plugs on most Douglas Fir Marine Grade plywood. Besides the poor visual appearance of the plug, that area tends to be structurally inferior to other areas that have not been repaired, especially for thinner sheets of plywood. The panels are sanded on both faces. The maximum core-gap size permitted is 1/8 inch, which also reduces structural performance. PS 1-95 Marine-grade plywood is available in 4x8-foot sheets of 1/4, 3/8, 1/2, 5/8 and 3/4-inch thickness. Sheets up to 5x12 feet are also available, but I've seen the factories use straight joint techniques versus angled scarfing to attain the longer lengths, making the joint weak for most structural applications requiring more than tensile strength. It is nearly impossible to get A-A grade Marine Fir these days. Most US mills produce AB due to the quality of logs that are available. Fir tends to be more brittle than other woods and the permissible defects make CNC work a challenge. I have seen 1/2" fir with 6 plies. Even numbered plies make an unbalanced panel that is more likely to warp. The thicker veneer composition increases stiffness, and flexibility is preferred on thinner panels.
Marine-grade plywood made to the BS1088 standard is typically available in Okoume, although, Meranti, Sapele, Agba, Khaya, Makore, Moabi, Movingui, Sipo-Utile and other African and Southeast Asian species have been used. Permissible species must meet the durability requirements within the standard.
BS1088 calls for the same tropical hardwood specie to be used throughout the panel; exterior glue (melamine or phenolic) for the core; no repairs on the faces; no core gaps or overlaps. BS1088 also requires an odd number of plies to be used. Regardless of the type of boat being made or application, using BS1088 plywood is by far easier to work with and priced competitively to the fir option.
What is Phenolic Glue?
Phenolic glue is one of the formaldehyde based family of adhesives commonly used in the production of marine, structural and exterior glued plywood. It is darker in color than MR (Moisture Resistant) adhesives, and thus may change the aesthetic of decorative panel products. Exterior Melamine, not phenolic glue, is typically used to adhere the face veneer to decorative exterior plywoods as the dark glue line may seep through the open grain of the face veneers.
What is PVA glue?
PVAs (Polyvinyl acetates) are the common white or yellow carpenter glues on the market. PVA has no added formaldehyde, is water based, and not as strong as a melamine Type I used in decorative marine plywood. PVAs, in production lines, are common for regular MR glued plywoods.
What is a composite panel?
A product consisting of wood, plant particles or fibers, bonded together by an adhesive such as a synthetic resin or binder. Examples include plywood, particle-board, OSB, and MDF. In marine applications, composite panels are FRP, End Grain Balsa core, Foam core, honeycomb core, Sound Deadening panels (with cork-rubber or revac core composition) or other such panels with plywood or FRP (Fiberglass Reinforced Plastic) skins.
What is Honeycomb core?
Available in nomex, aluminum, plastics or other materials, this geometric pattern is used in the marine and transportation industries as an excellent lightweight alternative to other products. Although it requires more preparation than plywood, it is lighter in weight and can out-perform other lightweight composite panels, depending on the specific function. When encapsulated in a laminate using a non-aqueous resin the scrim forms a seal limiting water migration through the structure, even if skin is punctured. It also has excellent impact resistance.
What is End Grain Balsa Core?
End-grain balsa is a structural core with properties that make it ideal for sandwich construction. It is compatible with all types of manufacturing processes from wet lamination to prepreg construction. Balsa is not affected by styrene or long resin gel times making it well suited for infusion applications. You can purchase rigid balsa sheets or contour cut with scrim as well as a variety of specialty cuts. Balsa is also available with a coating that minimizes resin absorption increasing bond strength and maximizing your weight savings. Today's balsa core is available with controlled density for making more precision parts and is an economical solution to higher priced foam cores. The typical density is 10lb although 7lbs densities are also available for a higher cost.
What is Foam Core?
Foam core panels can be made with a variety of different plastics: polyurethane, polystyrene, poly-vinyl chloride (PVC), etc. Closed cell foams are preferred in marine applications as they do not absorb or retain moisture. These panels may be made with plywood or FRP skins and are available in a variety of thicknesses and sizes.
What is FRP?
Fiberglass Reinforced Plastic. Since the introduction of other fiber reinforcement, FRP is also used to mean fiber reinforced plastics. Other terms that are used interchangeably with FRP are reinforced thermoset plastic (RTP), reinforced thermoset resin (RTR) and glass-reinforced plastic (GRP). All of the above mentioned terms should not be confused with reinforced thermoplastic which is entirely different. There is a wide selection of thermoset resins available for most corrosion resistant applications. Unlike thermoplastics, thermoset plastics have a highly crosslinked molecular structure. The result is a flexural, tensile strength, and temperature performance that is twice that of most thermoplastics.
What is MDF?
Medium Density Fiberboard is an engineered wood product made from wood fiber bundles and resin, extruded onto a conveyor in a "mat" form then pressed to a given thickness. MDF provides a smooth surface, but like particleboard it is denser and heavier than veneer core. MDF is not typically used in marine applications.
What is Particleboard?
Particleboard is an engineered wood product manufactured from wood chips and a resin, which, like medium density fiberboard is heavier and does not have the strength of veneer core plywood. Particleboard is a type of composite panel, but it is made up of larger pieces of wood rather than fiber bundles as used in MDF. Particleboard also provides a smooth surface, but does not have the strength of veneer core plywood, and because of the coarse nature of the particles, the edges must be treated in some fashion in the finished product. Particleboard is not typically used in marine applications.
What is OSB?
Oriented Strand Board is an exterior (phenolic bonded)
engineered wood product made by layering strands of
resin saturated wood on a mat with a specific orientation
that approaches veneer core in stiffness. It is frequently
used in the construction of new residential homes as a wall
and roof sheathing and as underlayment in certain cases.
OSB is not typically used in marine applications.
What is Veneer Core?
Veneer core is comprised of layers of relatively thick veneers peeled from hardwood or softwood species. These veneer layers (or plies) are typically laid up and balanced in alternating cross bands for stability and strength in 90 degree angles. Any decorative thin face of a wood species can be applied to the front and back of the panel. Compared to MDF and particleboard cores, veneer core offers strength, weight and screw-holding advantages.
What is Rotary Cut?
Rotary cutting is a method used to peel a log into thin sheets of wood as if unrolled from a spool, like paper towels . Rotary cut veneer has a variegated grain appearance, and can vary tremendously, although it is the preferred method to obtain large sections of wood to manufacture whole piece faces in standard and oversize structural marine grade panels. It is usually the least expensive veneer style.
Rotary cutting is the only way to achieve a 48" wide whole-piece face.
What is Quarter Cut?
Quarter slicing (also known as Quarter Sawn, Quarter Cut or Quartered) is a cutting method that involves dividing the log into quarters and slicing the quarter log on a radial direction approximately perpendicular to the growth rings to produce a straight grain appearance with the flake from the wood rays typically exaggerated on the surface. It is commonly used with red and white oaks because of the desired flake effect, but may be used on any species. Avoiding the flake effect and obtaining tighter grain appearance calls for a rift cut
What is Rift Cut?
Rift Cut Veneer is commonly produced in the various species of Oak. Oak has medullary ray cells which radiate from the center of the log like the curved spokes of a wheel. The rift ocomb grain effect is obtained by cutting at an angle of about 15% off of the quartered position to avoid the flake figure of the medullary rays.
What is Plain Sliced?
Plain slicing (also known as Plain Sawn or Flat Cut) a log produces thin veneers that are no wider than the log and have a pronounced repeating grain pattern. These pieces must be combined to make a plywood face by "matching" the pieces as desired by the customer.
What is Matching?
Matching is a term typically used in reference to the relationship between one veneer strip or "component" and the adjacent component in a face consisting of more than one component. The individual components are spliced together employing one of a number of matching techniques. The most common isbook matching, which requires reversing every other component as if you were opening the pages of a book. The result is a mirror image at the splice line.
Slip matching involves splicing each veneer to the next without turning over any component. This allows the face to have the tight side of the veneer out on each component, which helps avoid the "barber pole" effect of book matching.
The term "matching" may also be used in reference to the relationship of all components within a panel face. Running matching means the outer components will not be the same width as the inner components due to jointing the log so as to produce the greatest yield. Running match will be provided unless otherwise specified. Balance matching requires all components to be the same width and Center matching requires that there be an even number of same width components. Because of final panel trimming, the outer components of both balance and center matched faces will be slightly narrower than the other components. Center Balanced is typically specified for doors, allowing best positioning/yield.
The term "matching" may also apply to the relationship of one panel to the next. Sequence matching means the panels are produced from faces that were kept in order and numbered during the manufacturing process.
What is the "Barber Pole" effect?
"Barber pole" refers to the alternating dark and light appearance that is occasionally observed in book matched veneer as a result of the different surface characteristics that exist between the tight side and loose side of a given veneer, especially noticeable after finishing. Barber pole effect can be avoided by using matching techniques that utilize tight-side-out assembly.
What is Tight Side and Loose Side?
Conventional means of peeling or slicing a log results in the development of minute fractures known as lathe checks on the side of the veneer adjacent to the knife and closer to the center of the log as the veneer was cut. The side of the veneer having the lathe checks is the loose side, while the opposite side is the tight side. The loose side will tend to absorb more finishing material than the tight side, which sometimes results in a dark/light appearance called the "barber pole" effect.
What is a Calibrated panel?
A calibrated panel is typically a veneer core panel whose core was produced in a separate step and sanded to strict thickness tolerances before the outer decorative veneers are applied. Natural variation such as density, moisture absorption, and physical properties, combined with manufacturing variation results in thickness fluctuations in all wood panels. Veneer core typically has more potential thickness variation than engineered cores. A calibrated panel is designed to provide even tighter tolerance restrictions.
LUMBER:
What is 4/4"?
Four-quarter (sometimes called four-fourths) is standard terminology for one inch thick rough sawn lumber, regardless of specie. This is typically the thinnest rough sawn lumber thickness. 4/4 is comprised of four 1/4" (.25) measurements. Thicknesses are increased in 1/4" increments. In metric, 4/4" or 1" is equivalent to 25.4 milimiters.
What is 5/4"?
Similar to the description above, but with five 1/4" increments, or .25x5 = 1.25", 5/4 or 1-1/4". 5/4" is typically used to describe this thickness.















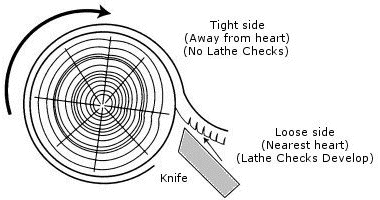